Solutions
Casestudies
Discover technical case studies showcasing how AI enhances engineering processes, automation, and decision-making. These studies explore different approaches to solving complex challenges through AI-driven methods.
Thank you! Your submission has been received!
Oops! Something went wrong while submitting the form.
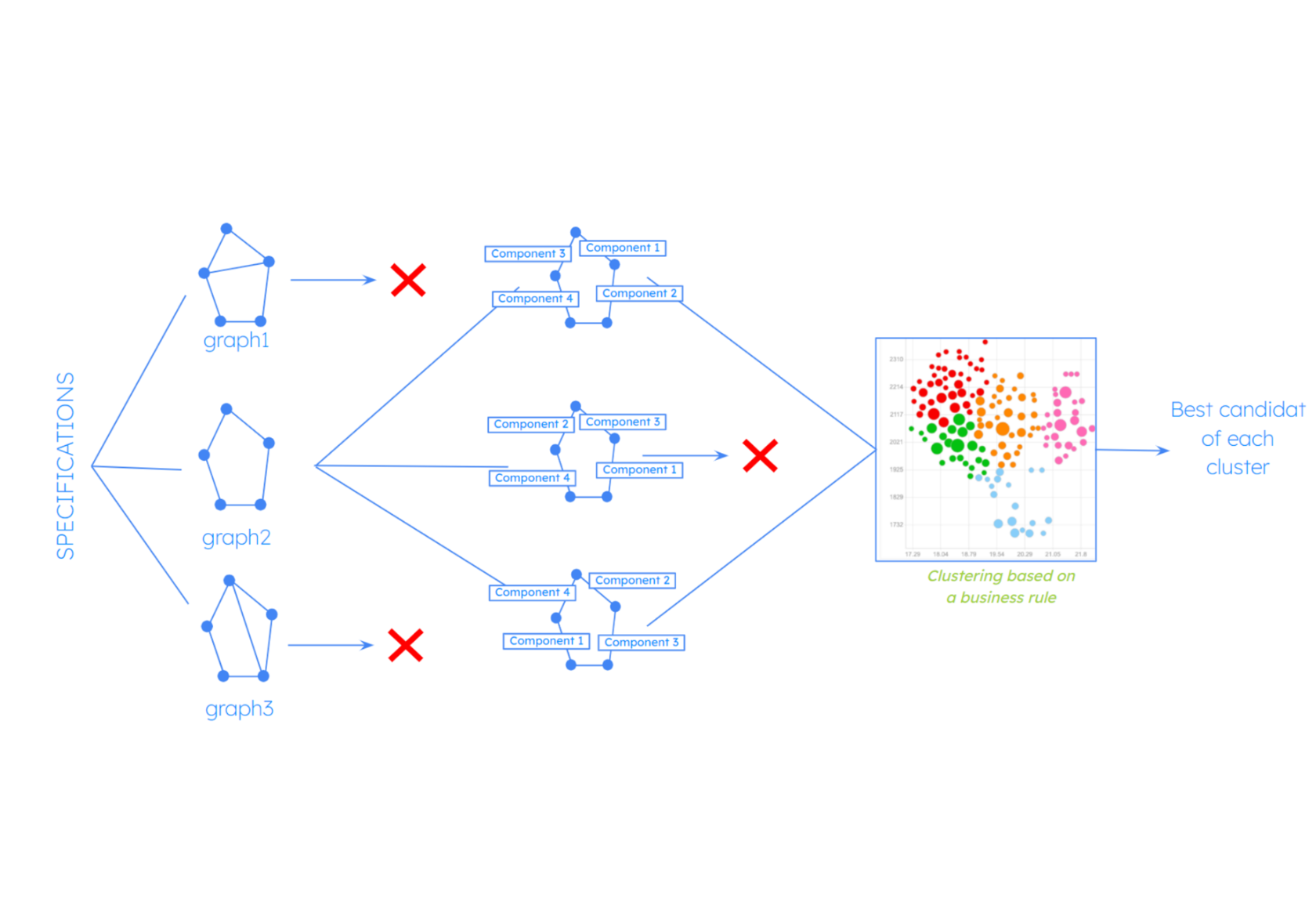
System Architecture Generation
April 2025
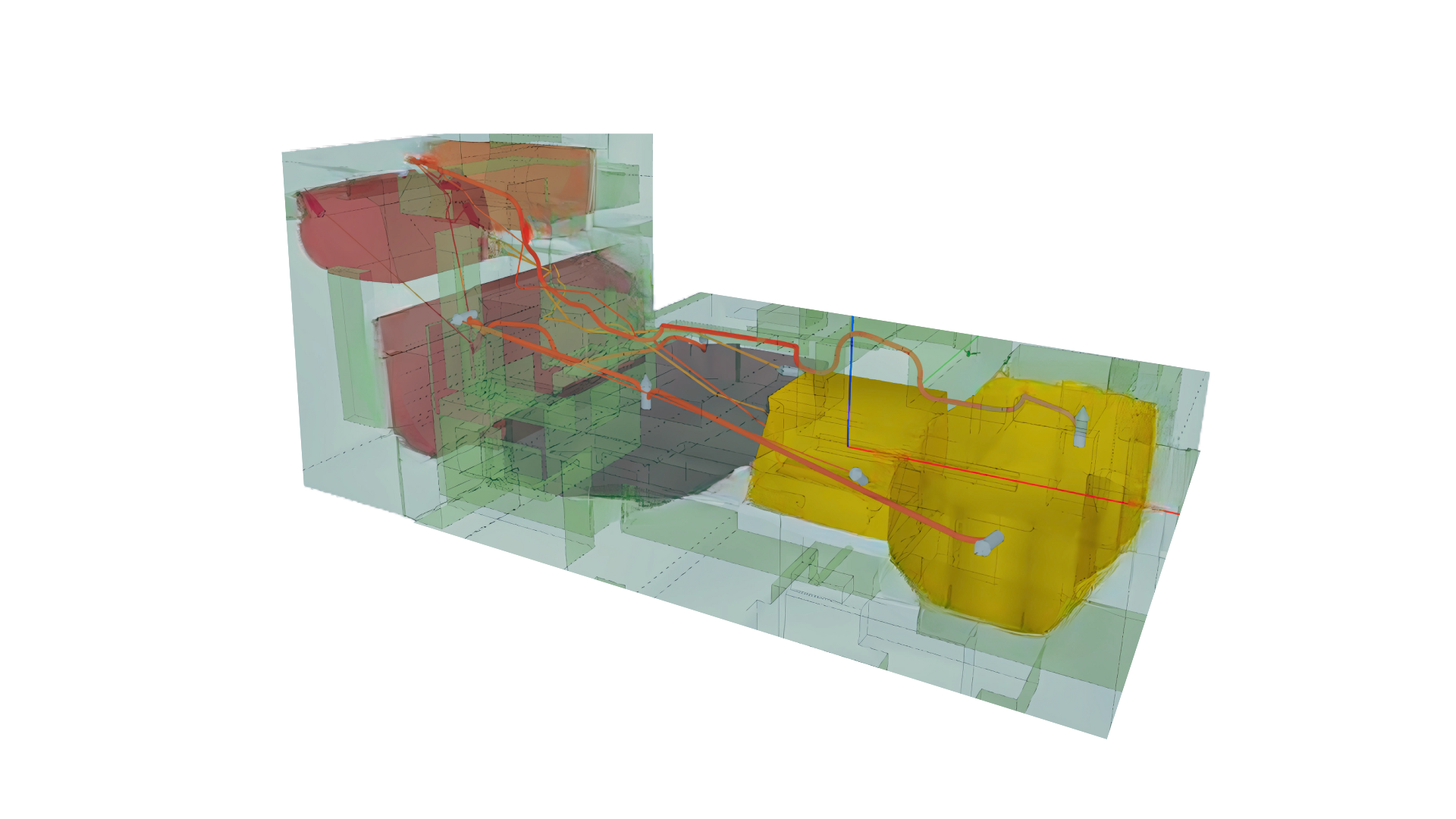
System Architecture Generation
April 2025
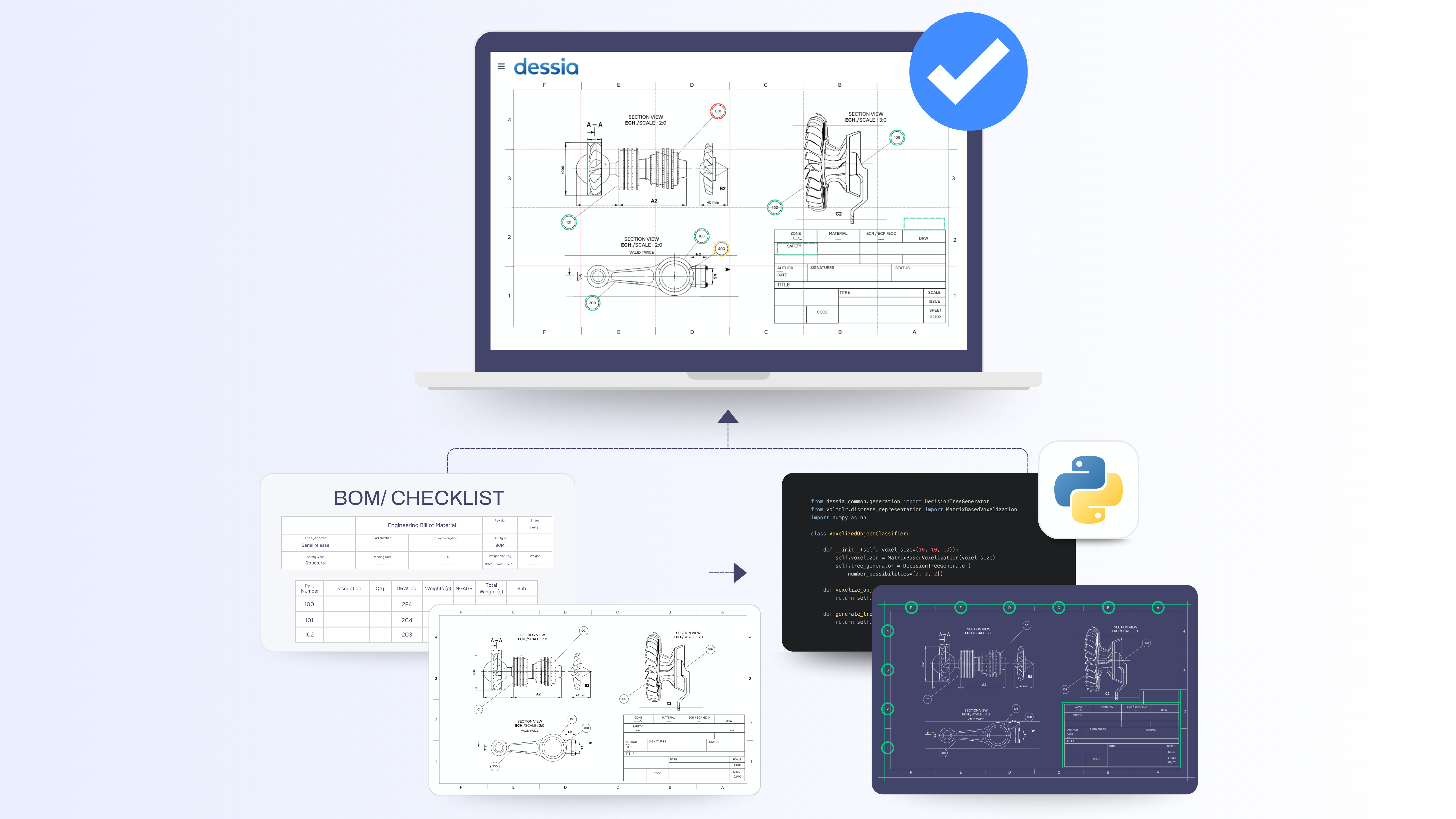
ContactUs
Contact us to see how you can streamline your design process.