Automated Industrial Plant Layout Digitalization
Automate 3D point cloud processing with AI to identify machines, rebuild plant layouts and deliver CAD-ready digital twins faster, smarter and at scale
Overview
Extracting actionable insights from 3D point cloud data—especially for component identification and layout reconstruction—is a complex and time-consuming task for many manufacturers. Despite the value of this data, traditional methods often struggle to deliver speed, accuracy, and scalability.
With Dessia’s AI libraries, manufacturers can automate the entire process of 3D point cloud classification and layout reconstruction. This case study illustrates how our solution reduces manual effort, enhances precision, and accelerates decision-making across production environments.
The challenge
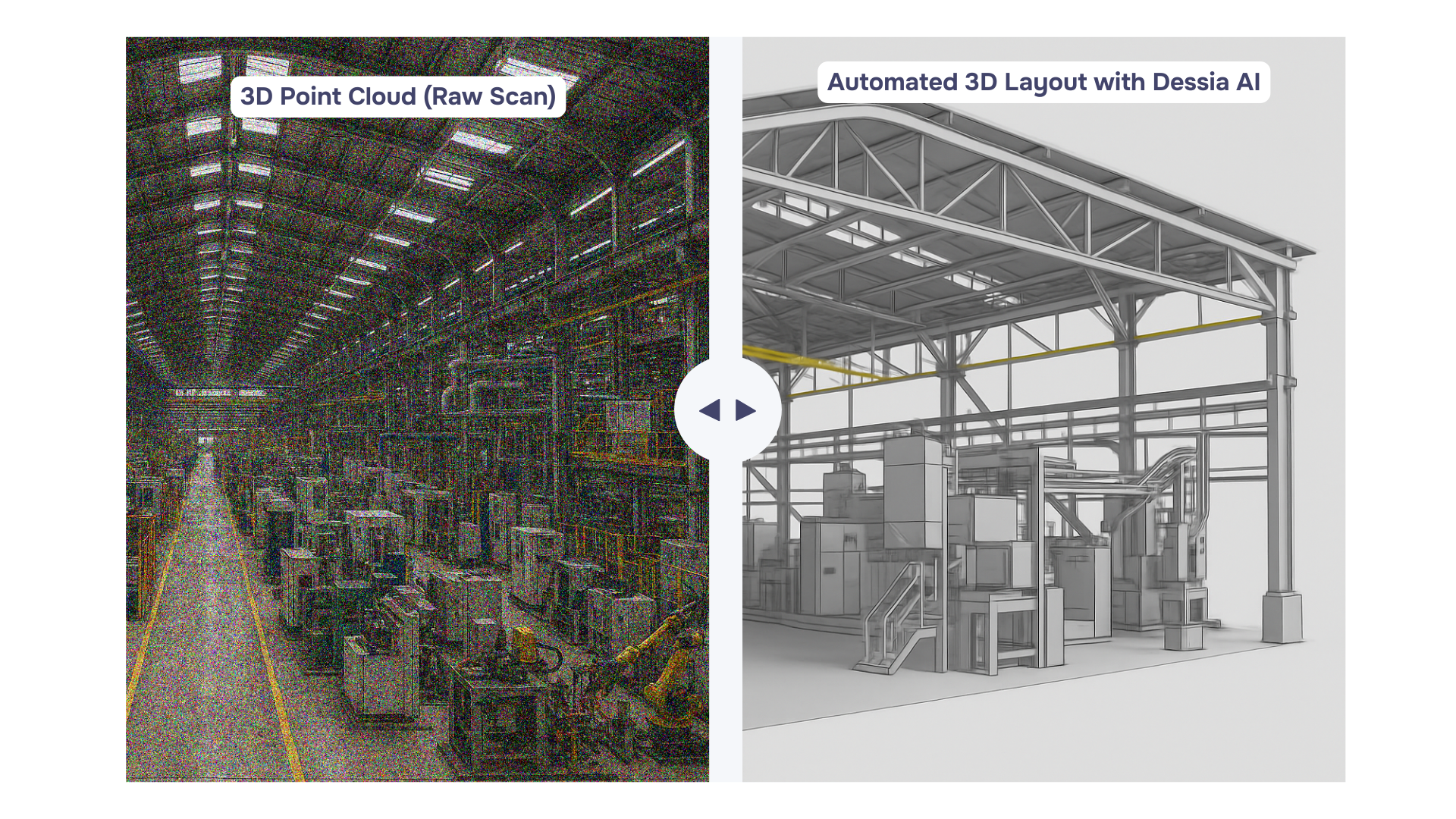
Imagine scanning a factory with a laser scanner: you get millions of 3D points, but no context.
- Which points belong to which machine?
- Where are the structures, racks, robots, or conveyors?
- How do you rebuild an accurate layout — without doing it manually?
Manual identification is slow, error-prone, and not scalable. Engineers can spend days or weeks labeling clusters and placing assets CAD models. The challenge was to automatically identify all known components from a 3D point cloud and rebuild the layout with precise positioning.
Dessia’s solution : Automated asset recognition
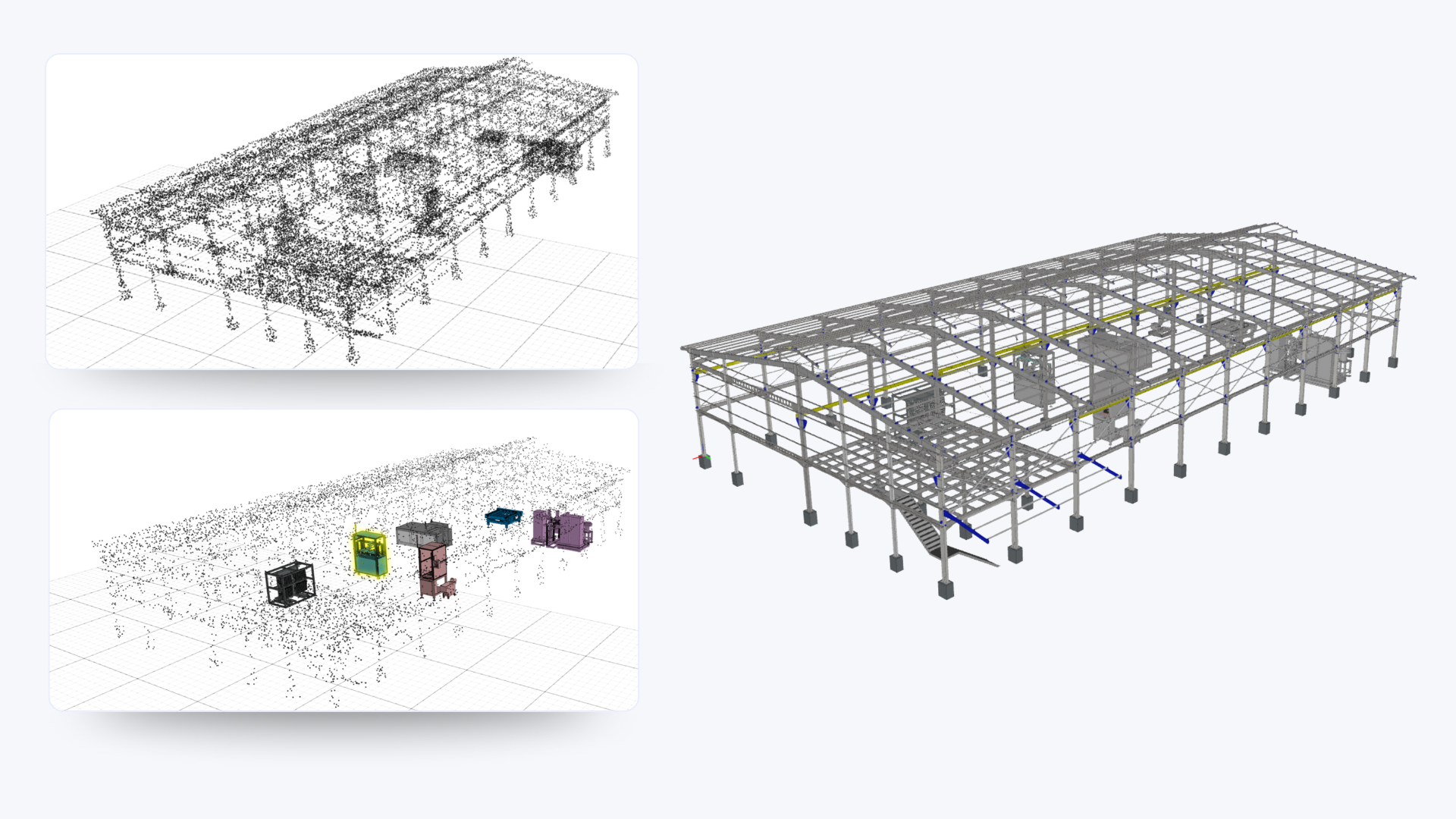
Dessia’s AI libraries automate the process of identifying machines and structures from raw 3D point clouds, transforming them into clean, structured layouts without manual intervention.
The process is structured into four key stages, designed to turn unstructured data into a clean, accurate digital layout.
1. Processing and structuring the scan
- The system begins by cleaning raw point cloud to remove irrelevant or noisy data.
- It then detects coherent groups of points that likely represent machines or fixed equipment.
- These groups are isolated and structured into clusters, giving shape to an otherwise chaotic dataset.
2. Aligning elements consistently
- Each cluster is adjusted to follow a uniform orientation and scale, removing inconsistencies introduced during scanning.
- This step ensures that components are evaluated within a consistent and neutral frame of reference, allowing them to be compared based purely on their shape and structure.
- As a result, the system improves the accuracy and reliability of the subsequent recognition process.
3. Recognizing known components
- The system compares each cluster to a predefined catalog of known machinery and equipment CAD Model.
- It identifies the most probable match based on the cluster’s overall shape and structural features.
- Once matched, the appropriate label or component name is assigned.
4. Reconstructing the 3D layout
- All identified components are reassembled into a full 3D layout of the scanned environment.
- Each item is placed in the correct position and orientation, reflecting its real-world arrangement.
- The final output is a structured, labeled digital twin — clean, usable, and ready for integration into planning or design tools.
This structured automation unlocks a faster, smarter way to transform 3D scan data into actionable layouts — reducing effort, accelerating decisions, and bringing clarity to even the most complex environments.
Outputs & results
The result is a fully reconstructed, structured 3D layout generated directly from the raw point cloud and component catalog.
The output includes:
- A reconstructed digital twin in which each machine and structure is correctly identified, positioned, and oriented
- Clear, standardized naming of all recognized components across the entire layout
- Exportable files in industry-standard formats — compatible with all major CAD tools and PLM platforms
- A layout that can be immediately used for design reviews, space planning, simulations, or asset tracking
This output provides not just a visual model, but a functional asset that enhances decision-making and operational planning, whether the process is executed directly within Dessia software or initiated from a third-party tool such as CAD or PLM systems.
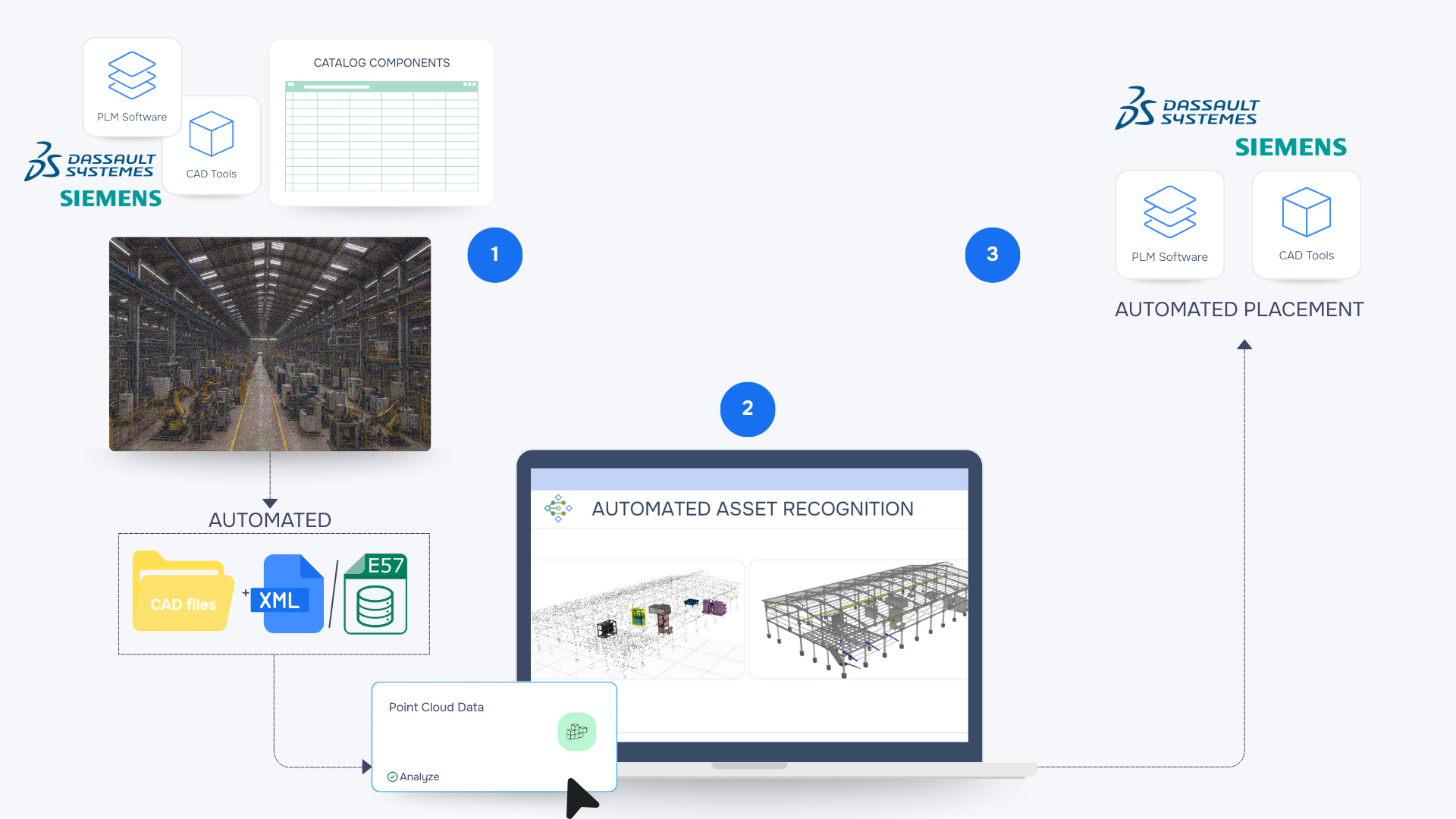
Conclusion
Dessia’s AI libraries offer a robust and scalable solution for transforming unstructured 3D scan data into structured, high-value digital layouts. By automating the identification, alignment, and reconstruction of known components, the platform replaces manual work with speed, consistency, and precision.
This solution removes the need for manual reconstruction, reduces delays, and gives teams reliable, organized data they can act on immediately.
Keep exploring - Discover more case studies
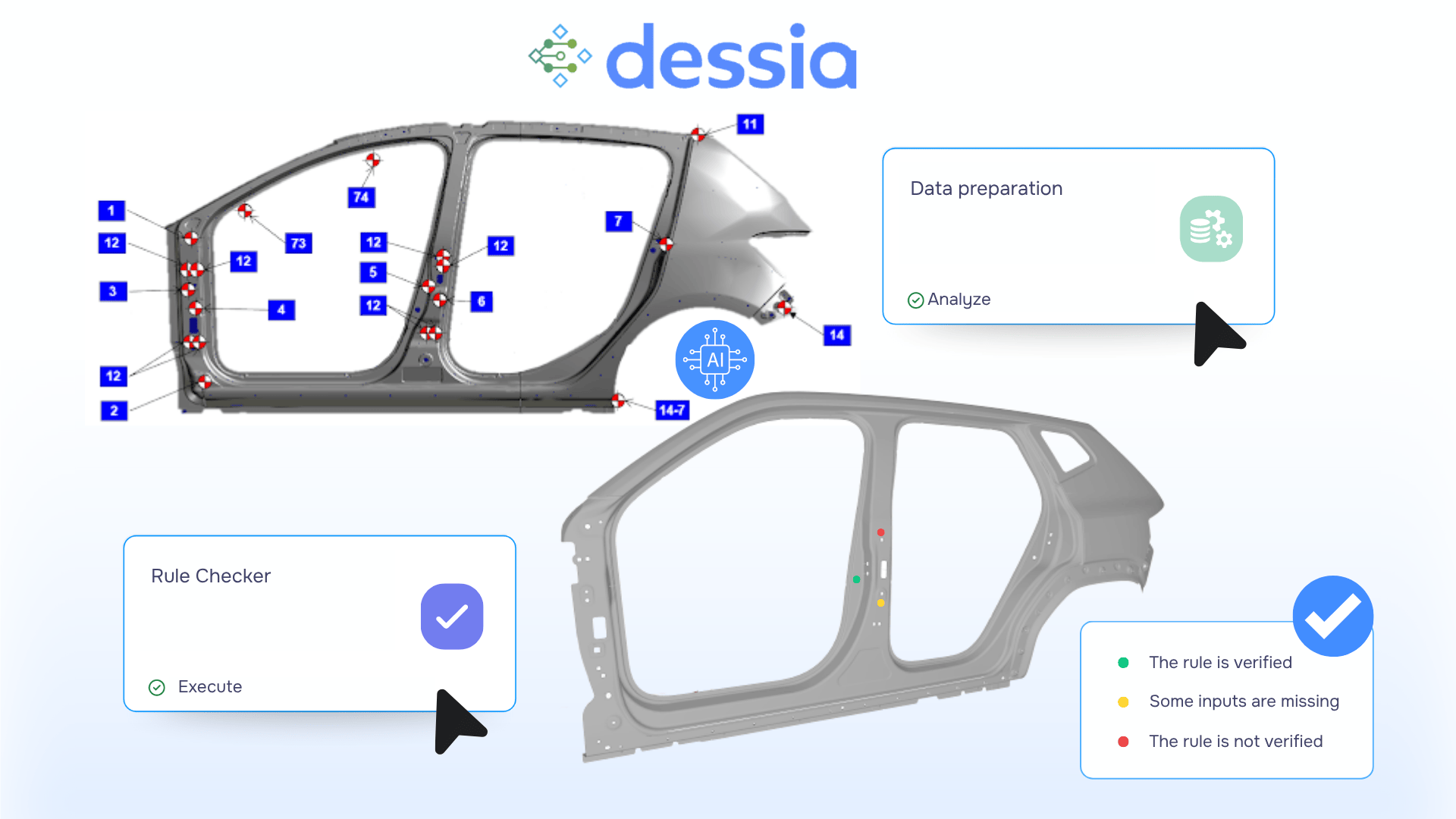

Mechanical Integration
11
min reading
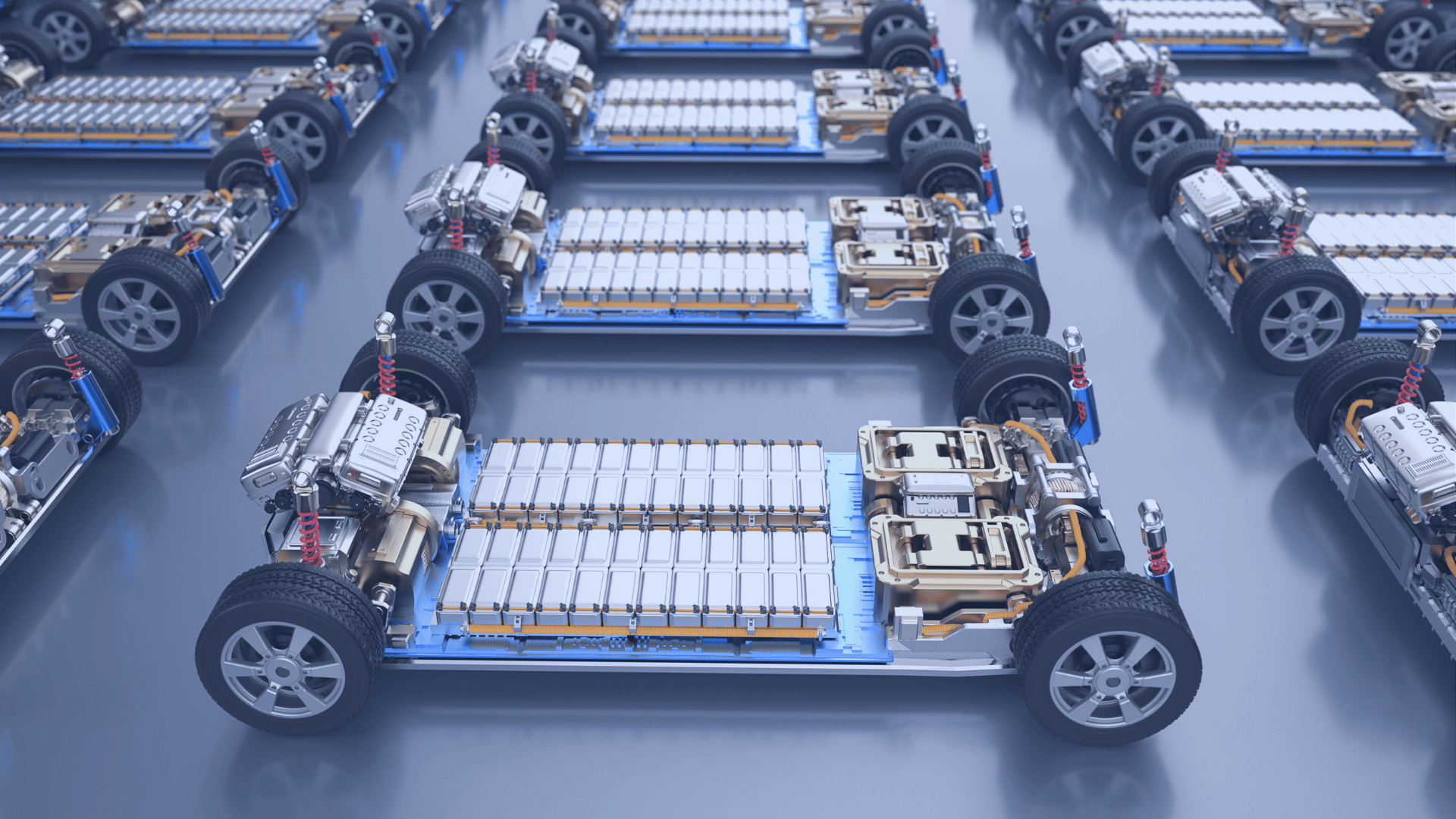